Integrating Advanced Machines in Dental Curricula
Integrating Advanced Machines in Dental Curricula
Blog Article
The world of dental care has actually experienced a cutting edge improvement over the last few years, with dental CAD/CAM (computer-aided design/computer-aided production) innovation at the forefront of this advancement. This state-of-the-art development employs innovative software application and precise equipment to design and manufacture dental restorations, such as crowns, bridges, inlays, veneers, and onlays. Dental CAD/CAM milling burs are an essential part in this procedure, playing an essential duty in shaping intricate dental repairs with remarkable precision.
Milling burs are reducing tools made use of together with dental milling machines to take and end up dental prosthetics from various materials. These devices should be sharp and exceptionally resilient, provided the precision needed and the solidity of materials they typically collaborate with. Common materials consist of metals, porcelains, and materials, although increasingly, zirconia has actually come to be the material of option for numerous dental restorations due to its premium strength, biocompatibility, and visual possibility.
Dental zirconia spaces, sometimes referred to as zirconia discs or blocks, are pre-manufactured types of zirconia utilized in the milling procedure. The manufacturing of dental zirconia begins with the formation of these blanks.
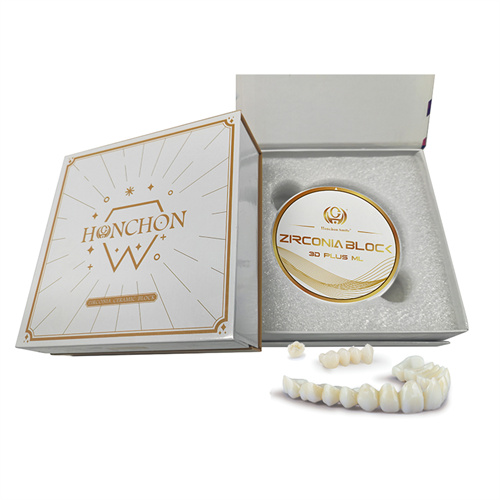
Explore the most recent improvements in dental CAD/CAM innovation, zirconia milling, and 5-axis dental milling machines that are changing corrective dentistry. Discover how developments like 3D plus Multiayer Blocks are improving precision, person, and effectiveness complete satisfaction in modern-day dental treatment.
Once the zirconia spaces are developed, they need to be sintered, commonly in a zirconia sintering furnace. Sintering is a thermal procedure developed to develop a solid mass from powder without melting it. During sintering, the zirconia fragments fuse with each other at high temperatures, enhancing the product's density and mechanical homes while accomplishing the desired clarity and color slopes. A zirconia sintering furnace is a customized tool efficient in obtaining the high temperatures needed for this process, commonly in the variety of 1350 ° C to 1600 ° C. The sintering procedure is crucial, as it maintains the zirconia structure and secure its biocompatible and visual high qualities.
Advanced milling makers, specifically 5-axis dental milling machines, have reinvented the manufacturing of dental remediations. Generally, dental reconstructions required labor-intensive processes and a significant quantity of time to generate. This gives the milling machine the versatility to come close to the zirconia blank from any kind of angle, which is critically essential for developing intricate shapes and undercuts properly and successfully.
Moreover, recent years have seen the intro of 3D plus Multilayer Blocks. These innovative materials integrate the advantages of multi-layered zirconia with the precision of 3D printing technology. The multi-layered element describes the slope in shade and clarity within the zirconia block, mimicking the natural shift from dentin to enamel discovered in genuine teeth. This slope result is attained by layering various shades and degrees of translucency of zirconia within the block during manufacturing. As a result, when this multi-layered block is crushed, the resulting reconstruction looks more lifelike and requires minimal post-processing or discoloring to match the client's all-natural teeth.
3D printing modern technology has actually included an additional layer of personalization and accuracy to this method. By integrating CAD/CAM styles with 3D printing, the elaborate details of the dental remediation can be captured and printed layer by layer. This leads to also greater precision in fit and looks, which is vital for individual fulfillment.
The mix of dental CAD/CAM systems, premium milling burs, dental zirconia blanks, innovative sintering heating systems, 5-axis milling machines, and the latest technology in 3D plus Multilayer Blocks exhibits the future of dental prosthetics. These innovations not only ensure accuracy and dependability however also simplify the production process, making it much faster and a lot more affordable. The causal sequence of these improvements spans much past makers and labs. Dental practitioners can provide much better service with quicker turn-around times, while clients take advantage of even more resilient, better-fitting, and cosmetically pleasing repairs. The shift from typical techniques to digital operations in dental methods highlights the action in the direction of improving precision, efficiency, and total client experience.
For example, the accuracy managed by these technologies suggests prosthetics can be developed and made with a high degree of accuracy, reducing the requirement for duplicated fittings or changes. This level of precision is largely driven by the high quality of dental CAD/CAM systems and the usage of premium milling burs capable of great outlining. Moreover, the handling of dental zirconia blanks in zirconia sintering heaters ensures that the end product meets the greatest criteria of sturdiness and biocompatibility.
The development of 5-axis dental milling equipments has widened the range of what is feasible in restorative dentistry. These equipments can mill complex geometries and fine details which were not feasible before, leading the way for more sophisticated dental services. This technical leap has likewise made it possible to utilize 3D plus Multilayer Blocks properly. These multilayer blocks offer natural-looking remediations that duplicate the rank of color and translucency discovered in actual teeth.
Furthermore, the continual growth in zirconia products and CAD/CAM technologies continues a much more efficient and reliable dental care atmosphere. Dental experts can currently accomplish more foreseeable outcomes, minimizing chair time and boosting person satisfaction. The comprehensive integration of these technologies into regular dental method indicates a seismic shift from responsive to aggressive dental treatment, where digital impressions, specific milling, and immediate adjustments end up being typical practice.
Another essential facet is the ecological and economic benefits these modern technologies bring. By lowering material waste and optimizing making use of resources, dental practices can operate more sustainably. The efficiency gains also translate into cost financial savings that can be handed down to individuals, making top quality dental treatment much more available. The global assimilation of these advanced materials and machines into dental curricula ensures that future dental specialists are skilled in the latest technical advancements, cultivating a culture of consistent enhancement and innovation.
In recap, the harmony between dental CAD/CAM systems, durable milling burs, top notch zirconia spaces, efficient zirconia sintering heating systems, advanced 5-axis dental milling makers, and revolutionary 3D plus Multilayer Blocks is driving a brand-new age in dental care. This combination is transforming exactly how dental restorations are created, fabricated, and implemented, causing better results for both dental experts and patients. As technology proceeds to advance, the future holds much more assurance for developments that will further transform dental treatment, making it more specific, effective, and patient-friendly than ever in the past. Report this page